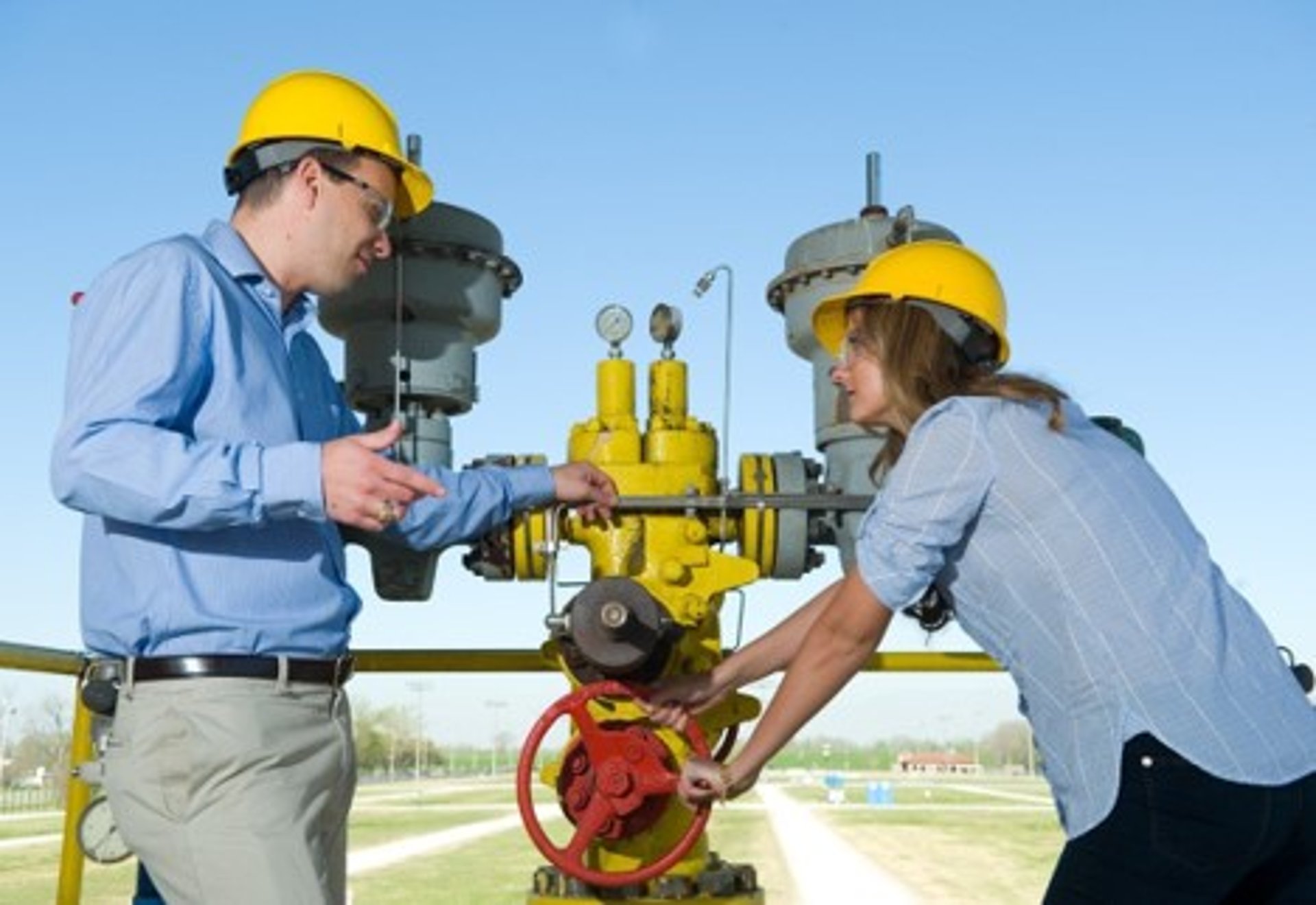
Hands-on Training
SBS Professional Consultants & Engineer understands that the complex operating environment these companies deal with also requires key support processes, which may include:
Preventive Maintenance
Calibration
Employee Certifications
Employee Competence and Training
Key Performance Indicators and Objectives
Supply Chain Management
We can customize any ISO/API or business process training to teach your staff what their responsibilities are in regard to the standards and the wellbeing of the organization. We can also provide additional training in the chosen standard to enhance employee understanding. Training can be instructor-led or through E-Learning, to guarantee training completion even in remote locations.
Quality Inspection Training
Overview
SBS Professional Consultants' Quality Inspection Training is designed to equip your team with the skills and knowledge necessary to conduct effective quality inspections. Our training program covers essential techniques, tools, and best practices to ensure that your products meet the highest standards of quality and compliance. This training is ideal for quality assurance professionals, production managers, and anyone involved in product quality control.
Training Objectives
- Skill Development: Enhance the skills and competencies required for effective quality inspections.
- Standards and Compliance: Understand industry standards, regulatory requirements, and customer specifications.
- Inspection Techniques: Learn various inspection techniques and tools used to assess product quality.
- Quality Control: Implement best practices for quality control and continuous improvement.
Who Should Attend?
- Quality Assurance Professionals
- Production Managers
- Quality Control Inspectors
- Manufacturing Engineers
- Supply Chain Managers
- Anyone involved in quality management and product inspection
Training Modules
1. Introduction to Quality Inspection
- Quality Basics: Understanding the fundamentals of quality and its importance in manufacturing.
- Inspection Roles and Responsibilities: Defining the roles and responsibilities of quality inspectors.
2. Industry Standards and Compliance
- Regulatory Requirements: Overview of key industry standards and regulatory requirements (e.g., ISO 9001).
- Customer Specifications: Understanding and meeting customer quality requirements.
3. Inspection Planning and Preparation
- Inspection Criteria: Defining quality criteria and acceptance standards.
- Inspection Plans: Developing effective inspection plans and checklists.
4. Inspection Techniques and Tools
- Visual Inspection: Techniques for visual assessment of product quality.
- Measurement Tools: Using calipers, micrometers, gauges, and other measurement tools.
- Sampling Methods: Understanding and applying statistical sampling methods.
5. Conducting Inspections
- In-Process Inspections: Techniques for inspecting products during various stages of production.
- Final Product Inspections: Conducting thorough inspections of finished products.
- Specialized Inspections: Handling inspections for specific requirements, such as first article inspection (FAI).
6. Data Collection and Analysis
- Documentation: Proper documentation of inspection results and findings.
- Data Analysis: Analyzing inspection data to identify trends and areas for improvement.
7. Reporting and Communication
- Inspection Reports: Preparing clear and detailed inspection reports.
- Communication Skills: Effectively communicating findings and recommendations to stakeholders.
8. Corrective and Preventive Actions
- Non-Conformance Management: Identifying and managing non-conformances.
- CAPA Processes: Implementing corrective and preventive actions to address quality issues.
9. Continuous Improvement
- Quality Improvement Tools: Using tools such as root cause analysis and Six Sigma for continuous improvement.
- Best Practices: Sharing industry best practices for maintaining high-quality standards.
Training Methodology
- Interactive Sessions: Engaging lectures and discussions to facilitate understanding of key concepts.
- Hands-On Training: Practical exercises and real-world scenarios to apply inspection techniques and tools.
- Case Studies: Analysis of case studies to illustrate successful quality inspection practices.
- Assessments and Feedback: Regular assessments to gauge participant understanding and provide constructive feedback.
Benefits of Our Quality Inspection Training
- Improved Skills: Enhance the inspection skills and capabilities of your team.
- Consistent Quality: Ensure consistent product quality through effective inspection practices.
- Regulatory Compliance: Maintain compliance with industry standards and regulations.
- Reduced Defects: Minimize defects and non-conformances through thorough inspections.
- Customer Satisfaction: Increase customer satisfaction by delivering high-quality products.
- Continuous Improvement: Foster a culture of continuous quality improvement within your organization.
Contact Us
For more information or to enroll in our Quality Inspection Training program, please contact us
SBS Professional Consultants
Your partner in quality inspection training and excellence.
SBS Professional Consultants & Engineer
No: 7, Navganesh Realities, Sivaprakasam Nagar, Surappattu, Chennai, Tamil Nadu, India. 600 066.
+91 8122642512 | +91 9043332524
support@sbsprofessionalconsultants.com
© 2024. All rights reserved.
Contact Us
Reach out to SBS Professional Consultants & Engineers for consultation, implementation, training, and audit services.
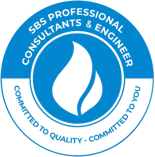
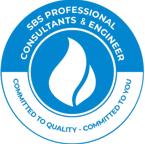